ONARCHITECTURE- Bricks and mortar? Council approves $7.5 mil Mall project
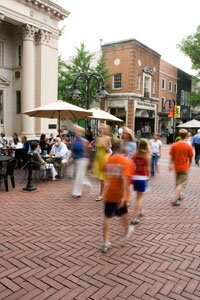
On July 21, despite the fact that over 70 percent of the bricks on the Downtown Mall are in good condition, City Council approved a plan to tear up the existing bricks and replace them between January and May 2009.
Well, it looks like you can kiss our Mall bricks good-bye– all 375,000 of them.
Despite an admission from Councilor David Brown that he's "cheap" and wishes the Mall could simply be fixed, a report from Councilor Holly Edwards that someone pleaded with her not to vote for the renovation because "it did not promote economic justice," concern from Councilor Satyendra Huja about what would happen to the old bricks, and some worries from Mayor Dave Norris about how to handle potential delays and unforeseen problems, City Council voted unanimously to move forward with a $7.5 million Downtown Mall renovation, $5 million of which will be used, beginning in January 2009, to pull up and replace the estimated 375,000 bricks.
(Edwards expressed her concern that "true employment opportunities" for local workers be provided with the renovation, and that "If the Mall needs to be developed, then affordable housing needs to be developed too.")
In addition, almost immediately after the vote, City Manager Gary O'Connell told Council and the assembled crowd that while the Mall bricking would begin in January, other "things are going to happen sooner than you think."
As chief planner Jim Tolbert explained, work will begin on repairing the drainage runnels– which will be constructed using 4" x 12" bricks in the current design, and set in mortar– in the coming months. Then replacement parts for the fountains will be ordered and the lighting repaired. After he gets final recommendations from the Board of Architectural Review in August, Tolbert said, the new bricks (Council wants to use the existing 4" x 12" size, if possible), bike racks, benches, and other materials will be ordered.
The vote came as a disappointment to UVA architectural historian Daniel Bluestone, who urged Council to handle the Mall's "long-differed maintenance problem" by hiring masons from the Charlottesville community who would reuse and repair the existing bricks, 80 percent of which, according to the City's own figures, are still in good shape. "The existing bricks on the Mall could be easily recycled and re-used," Bluestone told Councilors.
Indeed, at a packed public meeting on the renovation last month– nearly 200 people showed up– a majority of speakers echoed Bluestone's sentiments, and wondered why the existing bricks on the Mall couldn't simply be fixed, both to save money and preserve the original Lawrence Halprin design.
"It scares me that you didn't think of reusing the existing brick," said one concerned citizen, his voice rising in indignation as he pointed out how many of the bricks are still in good condition. Charlottesville resident David RePass said that the idea of replacing the entire Mall with sand-set bricks "should make everyone in Charlottesville bristle" because it would give the Mall a "pattern-less surface" and look "sterile and boring." He, and others, hoped the existing mortar-set, herringbone pattern could be preserved.
Oddly enough, Brown's comment about being cheap was the only reference by any of the Councilor's to the concerns about money expressed at the public meeting. Instead, Councilors focused on what to do with the discarded brick, on the possibility of using local labor, on brick size, and on the proposed "corrals" to conceal newspaper boxes. In fact, discussion of the corrals was the most contentious, with Huja calling the current news box arrangements "hideous," Councilor Julian Taliaferro calling them "tacky," Brown saying he likes them the way they are, and Norris bristling at the idea of spending $50,000 for "government newspaper corrals."
Surprisingly, though, there wasn't much bristling about spending $5 million for news bricks, only a kind of sighing aside from Edwards, "We're never going to get over how much this costs."
One of only three amendments to the approved resolution included further discussion of the news box corrals. There was no discussion of the possibility of repairing and reusing the existing bricks.
When asked, Tolbert said that no decision had been made about what to do with the existing bricks. He paid lip service to perhaps selling or offering them to the public, but it was clear that the five-month time-table for the project will not allow for careful handling of the bricks.
In all likelihood it appears the existing bricks are headed for a grinder or a scrap heap somewhere.
Indeed, Brandie Schaeffer, a representative for the Brick Industry Association, who has lately been advising City planners on the project, said the construction would likely damage or destroy most if not all of the existing brick, as properly preserving them would require slow and carefully removal, an unlikely scenario given the City's wish to have the project completed in five months.
Wait a minute– it's not about the bricks?
For months, indeed years, the discussion of a possible Mall renovation has been focused on the bricks–their historic and architectural significance, their poor condition, whether repairing them or replacing them is the best option, and whether setting them in sand or with mortar is the best method.
However, in a conversation with the Brick Industry's Schaeffer shortly after Council's decision, she revealed something startling– we may have been discussing the wrong thing all along.
"The bricks are not the problem," she said. "What's underneath them is."
According to Schaeffer, it's the method in which the original bricks were laid that has caused the mortar to crack and the bricks to shift. In the 1970s, it was common practice to install brick pavements on a "dry pack" bed on top of a concrete slab, the method Schaeffer believes was used to lay the bricks on the Mall. The dry pack bed was a 1:5 mixture of cement and sand with just a little water mixed in. The cement and sand were usually mixed dry, leveled on the ground, watered, packed and rolled. Then the brick paver was set on it. Unfortunately, this method did not create a strong enough bond between the brick and its setting, and over time many projects carried out this way have deteriorated.
Gary Davis, a masonry expert with Endicott Bricks in Nebraska, concurs, based on his experience with numerous projects from the 1970s.
Schaeffer and Davis say the proposed plan to use 4" x 12" bricks set in sand could be a mistake, as the sand bed will erode and shift over time, as water inevitably gets below the brick to the sand level, causing the brick to tip and tilt. In addition, while the bricks themselves are strong and stable, because they're longer, the lack of a firm setting would make them more easily susceptible to breakage.
But as Schaeffer concedes, no one she knows has ever tried to set this many 4" x 12" brick pavers in sand, so theories about these negative effects are just speculation. "We would definitely be interested in monitoring this project as a test case," she says.
Throwing a wrench into the proposed plan to use 4" x 12" bricks set in sand, Davis recommends a mortar setting bed installation. "The best mortar mix now," says Davis, "one that is durable, hard, water resistant and bonds strongly, includes Portland cement, sand, water and a latex additive."
After the bricks are removed, one coat of this mortar bed would be laid down on the concrete slab to level it– it will probably be roughed up after the removal of the existing brick and mortar– and to get the proper sloping for drainage. Then a second coat would be laid and the bricks set into it. After the bricks have set, either mortar or sand could be used to fill the joints.
Basically, both Davis and Schaeffer are saying the bricks are beside the point– it's how they are laid that matters. If Councilors are set on keeping Halprin's 4" x 12" brick size and pattern– and it now appears they are– they might be wise to lay them in a mortar bed, a process that could take much longer than planned, but one that might be more cost-effective, safe, and durable in the long run.
#